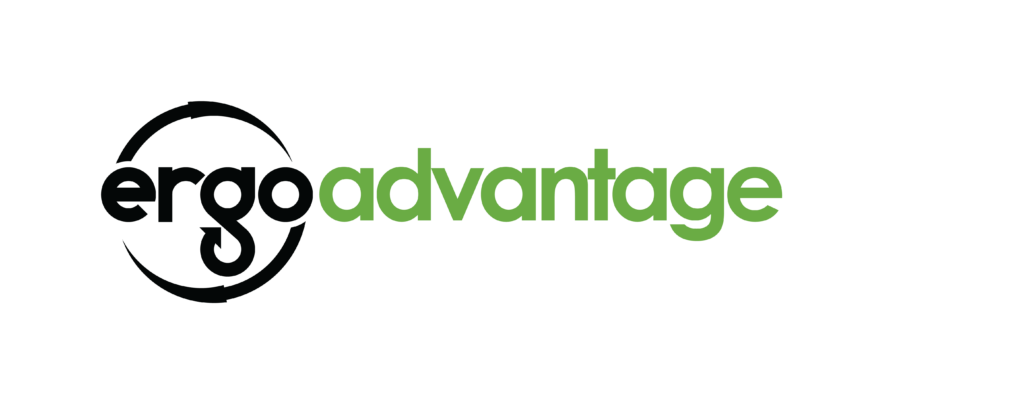
PPE: Understanding the Gear that Keeps Workers Safe
Personal Protective Equipment (PPE) keeps workers safe from the many injuries and illnesses that can occur in the workplace – from noise and mechanical hazards to chemical, radiological, electrical, and beyond. In this article, we’ll explore the important role PPE plays in workplace safety, as well as OSHA’s equipment standards and training recommendations.
An Overview of PPE
After workplace hazards have been mitigated as much as possible through engineering and administrative controls, PPE is a worker’s last line of defense. For instance, danger can be directly mitigated by building a barrier between workers and hazards or rotating workers so they don’t spend too much time in hazardous locations. But wherever these interventions aren’t feasible or don’t provide sufficient protection, PPE enters the scene.
Any type of personal equipment used to protect someone from hazards falls under the PPE umbrella, including gloves, safety glasses, footwear, hearing protection, hard hats, respirators, coveralls, vests, full-body suits, and more. In one workplace, implementing PPE might entail full-body protective gear that keeps workers safe while working with hot substances, while in another, it might entail the use of hearing protection to prevent permanent hearing loss.
Here are the major hazards PPE is used to address, according to OSHA’s Personal Protective Equipment publication:
Eye & face protection from “flying particles, molten metal, liquid chemicals, acids or caustic liquids, chemical gases or vapors, potentially infected material or potentially harmful light radiation.”
Head protection from objects falling from above, low-hanging objects like beams and pipes, or the possibility of a worker’s head coming into contact with an electrical hazard.
Foot & leg protection from “falling or rolling objects or from crushing… penetrating materials… exposure to hot substances or corrosive or poisonous materials” or electrical hazards.
Hand & arm protection from “skin absorption of harmful substances, chemical or thermal burns, electrical dangers, bruises, abrasions, cuts, punctures, fractures and amputations.”
Body protection from “cuts and radiation… temperature extremes; hot splashes…; impacts from tools, machinery, and materials; hazardous chemicals.”
Hearing protection from “noise level, as measured in decibels… duration of each employee’s exposure to noise… whether employees move between work areas with different noise levels… whether noise is generated from one or multiple sources.”
Personal fall protection systems to “provide protection from falling or to safely arrest an employee’s fall if one occurs.”
Employers must perform a PPE Assessment to identify potential hazards in their workplace and select protective gear that will protect workers from them. Each work environment poses unique risks, such as falling objects, sharp tools, chemical exposure, and loud noises. Without a proper assessment, workers may face unnecessary danger. However, this risk of injury can be greatly reduced by equipping workers with the proper gear, such as helmets, gloves, or hearing protection.
PPE Training
To ensure effective protection, PPE must be properly fitted, maintained, and used. If protective equipment doesn’t fit workers, it can’t keep them safe from hazards. Likewise, if PPE isn’t cleaned, evaluated, maintained, or disposed of, it can’t reliably protect workers either. Even if PPE is well-fitted and kept in great shape, it’s just as important to ensure workers have a clear understanding of why and how it’s used.
This will require training in language that workers understand, as well as retraining for workers who demonstrate an improper understanding of the equipment. OSHA recommends that PPE training should cover…
How to put on, adjust, and use PPE;
How PPE protects from certain hazards;
The hazards from which PPE cannot protect;
The useful life, disposal, and maintenance of PPE.
OSHA Standards
Employers are required to determine if hazards are present in the workplace and provide the necessary PPE to prevent harm wherever it cannot be mitigated by physical or administrative changes. Once PPE is selected, employers must ensure it’s properly maintained and fits each worker. Employers must additionally ensure all workers understand how and why PPE is so important through continual training and retraining.
For many categories of PPE, OSHA requires equipment to meet or be equivalent to the following American National Standards Institute (ANSI) standards (for an interactive table, you can visit OSHA’s PPE Standards page):
Eye and Face Protection: ANSI Z87.1-2010, ANSI Z87.1-2003, or ANSI Z87.1-1989(R1998).
Head Protection: ANSI Z89.1-2009, ANSI Z89.1-2003, or ANSI Z89.1-1997.
Foot Protection: ASTMF-2412-2005 and ASTMF-2413-2005, ANSI Z41-1999, or ANSI Z41-1991.
Electrical Rubber Insulating Equipment: ASTM D120-09, ASTM D-178-01 (2010), ASTM D-1048-12, ASTM D-1049-98 (2010), ASTM D-1050-05 (2011), or ASTM D1051-08.
Where Can I Learn More?
OSHA PPE Standards
OSHA’s PPE Fact Sheet and Online Guide