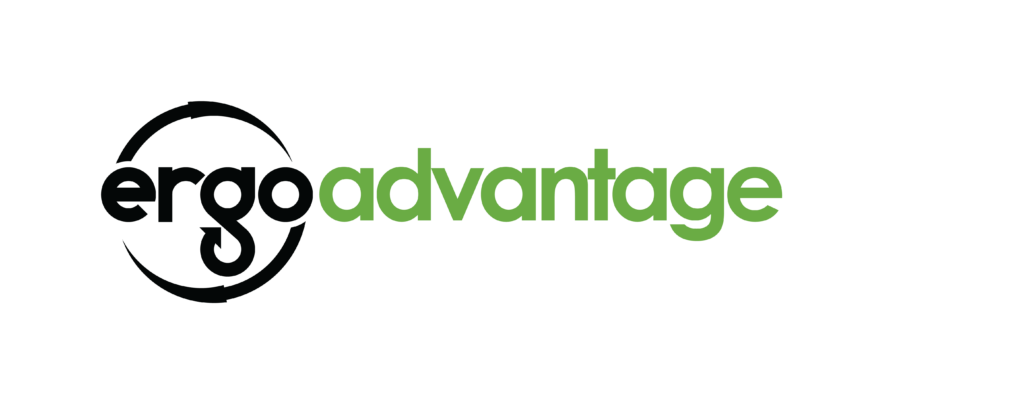
Machine Guarding: Preventing Hands-On Hazards
The powerful machinery that makes manufacturing so efficient can just as easily cause life-changing injuries to those who operate it – unless the right protections are in place. In this guide, we’re going to explore the role machine guarding plays in injury prevention and then take a closer look at OSHA’s requirements for these safeguards.
Injury Prevention
Amputations, deafening noise, thermal burns, electrocutions – there’s no shortage of machine-related injuries that can be inflicted by moving machine parts. Machine guarding is one of many safeguards that minimize this risk by:
● Preventing contact to ensure operator body parts don’t touch dangerous elements of a machine, including sparks and chips ejected from the machine.
● Minimizing other hazards, such as catching objects that might otherwise fall into moving parts and become projectiles.
● Enhancing efficiency by ensuring the safeguard is easy to work with and doesn’t slow down production.
In the “Machinery and Machine Guarding” subpart of OSHA’s Occupational Safety and Health Standards, examples of machine guarding include “barrier guards, two-hand tripping devices, electronic safety devices, etc.” OSHA additionally recommends the use of indirect aids, though only “to supplement protection provided” by machine guarding, such as an “awareness barrier” that reminds workers when they enter a danger zone.
Of course, even the most advanced safety system will become ineffective if workers aren’t sufficiently trained to use it. Wherever machines are being operated, ensure operators and workers in the vicinity have a clear understanding of all possible hazards associated with the machine, how safeguards protect them, and how to recognize when safeguards are damaged or missing.
Types of Machine Guarding
Different types of machine guarding provide protection from hazards unique to certain machines and settings. Here’s an overview of the three major types:
● Fixed: A permanent part of the machine that acts as a barrier, often constructed of sheet metal, screen, wire cloths, bars, or plastic.
● Interlocked: A removable guard that automatically shuts off machinery until it’s put back in place. For instance, an interlocked guard could allow workers to efficiently clear a jam within the machine without the difficulty of removing a fixed barrier.
● Adjustable: A barrier that can be adjusted to provide optimal protection from varying sizes of stock entering the danger area.
OSHA’s Machine Guarding Requirements
Here are a few highlights from OSHA’s machine guarding requirements – not to be taken as a comprehensive summary:
● “Guards shall be affixed to the machine where possible…” Ideally, machine guarding will be directly attached to the machine, only secured elsewhere when direct attachment isn’t possible.
● “Revolving drums, barrels, and containers shall be guarded by an enclosure…” particularly an enclosure that’s “interlocked with the drive mechanism,” so containers can’t revolve until the guard enclosure is in place.
● “When the periphery of the blades of a fan is less than seven (7) feet above the floor or working level, the blades shall be guarded.” Additionally, the fan guard shouldn’t have openings that exceed one-half inch.
Where Can I Learn More?
1. OSHA’s machine guarding eTool
2. Industry-specific guides to OSHA’s machine guarding standards.